Basics of Cost Management
The costs associated with a manufacturing firm are separated into two broad categories. These include manufacturing costs and selling & administrative costs (G&A - General and Administrative). This functional separation is important because each category of cost is treated differently in the accounting records. The different treatments are required to obtain proper matching.
Manufacturing Costs
There are three types of manufacturing costs. These include:
1) Direct material or raw material,
2) Direct labor, and
3) Out side processing
4) Indirect manufacturing costs, or factory overhead.
Direct material becomes the product, or becomes a part of the product. Direct labor converts the direct material into a finished product. Factory overhead represents all the other factory costs that cannot be directly identified with a particular product. This indirect category includes a variety of costs that are discussed in more detail in subsequent chapters. These three types of costs are also referred to as product costs, or inventoriable costs, because they are capitalized in (or charged to) the inventory, i.e., they become assets.
Matching
Accountants capitalize manufacturing costs to obtain proper matching. The matching concept is pervasive in accrual accounting and requires that costs and benefits are matched or brought together on the income statement. In a production setting, the idea is to match the costs of producing a product (or service) against the benefits, i.e., revenue derived from the sale. When the inventory is sold, these costs are charged to an expense account referred to as cost of goods sold. At the end of the accounting period, cost of goods sold is closed to the income summary where, theoretically, matching takes place.
Remember that unexpired costs represent assets. Expired costs represent expenses. When the inventory is sold, we say these costs have expired, i.e., the benefits to be obtained (from the effort that generated the costs) have been recognized. Thus, manufacturing costs become expenses when they reach cost of goods sold, but represent assets until the sale takes place.
Selling and Administrative Costs
In traditional accounting systems , selling and administrative costs are expensed in the period in which they are incurred. Theoretically, if there are future benefits associated with a cost, the cost should be capitalized as an asset rather than expensed. Certainly there are some future benefits associated with costs such as research and development, training, market promotion and advertising. However, these costs are expensed as incurred because it is difficult if not impossible to relate them to the future benefits. As a result, these costs are referred to as period costs.
COST BEHAVIOR AND PREDICTION
In addition to separating costs into categories such as direct and indirect and manufacturing and non-manufacturing, costs are also frequently identified by their behavior in relation to changes in an activity level. This separation is helpful for planning and budgeting purposes. The major types of costs, in terms of cost behavior, are:
1) variable costs,
2) fixed costs,
3) semi-variable costs and
4) semi-fixed costs.
COST ACCOUNTING SYSTEM
A cost accounting system requires five parts that include: 1) an input measurement basis, 2) an inventory valuation method, 3) a cost accumulation method, 4) a cost flow assumption, and 5) a capability of recording inventory cost flows at certain intervals. Note that many possible cost accounting systems can be designed from the various combinations of the available alternatives, although not all of the alternatives are compatible. Selecting one part from each category provides a basis for developing an operational definition of a specific cost accounting system.
INVENTORY VALUATION METHODS
The four inventory valuation methods that appear in below fig. are arranged in the order of the amount of cost that is traced to the inventory. The throughput method involves tracing the least amount of cost to the inventory, while the activity based method includes tracing the greatest amount of costs to the inventory. In direct (or variable) costing, a greater amount of cost is traced than in the throughput method, but a lesser amount than in the full absorption method. Direct costing and full absorption costing are the traditional methods, while the throughput and activity based methods are relatively new. These inventory valuation methods are very important because they control the manner in which net income is determined. Oracle provides full absorption method.
Absorption Costing or Full Costing System:
Absorption costing is a costing system which treats all costs of production as product costs, regardless weather they are variable or fixed. The cost of a unit of product under absorption costing method consists of direct materials, direct labor and both variable and fixed overhead. Absorption costing allocates a portion of fixed manufacturing overhead cost to each unit of product, along with the variable manufacturing cost. Because absorption costing includes all costs of production as product costs, it is frequently referred to as full costing method.
Variable, Direct or Marginal Costing:
Variable costing is a costing system under which those costs of production that vary with output are treated as product costs. This would usually include direct materials, direct labor and variable portion of manufacturing overhead. Fixed manufacturing cost is not treated as a product costs under variable costing. Rather, fixed manufacturing cost is treated as a period cost and, like selling and administrative expenses, it is charged off in its entirety against revenue each period. Consequently the cost of a unit of product in inventory or cost of goods sold under this method does not contain any fixed overhead cost. Variable costing is some time referred to as direct costing or marginal costing. To complete this summary comparison of absorption and variable costing, we need to consider briefly the handling of selling and administrative expenses. These expenses are never treated as product costs, regardless of the costing method in use. Thus under either absorption or variable costing, both variable and fixed selling and administrative expenses are always treated as period costs and deducted from revenues as incurred.
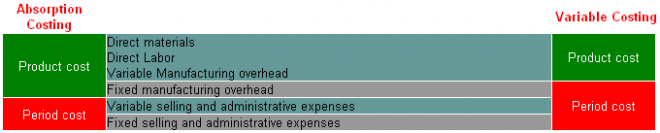
InVENTORY COST FLOW ASSUMPTIONS
A cost flow assumption refers to how costs flow through the inventory accounts, not the flow of work or products on a production line. This distinction is important because the flow of costs is not always the same as the flow of work.
At first glance, you may see no nedd to make an assumption about how costs flow through the inventory account. The cost of each item placed in the physical inventory can be entered into the account, and then, as the item is physically taken from inventory, the cost can be removed from the account.In this way, the cost accumulated in the account can be perfectly match the items physically held, and the cost of goods sold can equal the sum of the cost of each item actually delivered to a customer. Such an inventory system can be identified as a specific identification system.
Specifically identifying each item in inventory is relatively easy if each item is unique, such as an art object or a piece of custom-made furniture, or if each item has an identification number, such as an automobile. However, specific indentification is not practical when inventory items are not individually identifiable. This is the case with bushels of wheat, caseloads of memory chips, and loads of brass hooks like the ones used in Amalgamated's hat racks. In these cases, accountants commonly assume a flow cost through the inventory account that is not necessarily related to the acctual physical flow of goods.
a) Average cost price items in inventory on the basis of the average cost of all similar goods available during the period.
b) Standard Price versus Average Price
With average price control, a new material price is calculatedafter every goods receipt, invoice receipt, and/or order settlement. This material price is an average value calculated from the total inventoryvalue and the total quantity of the material in stock.
With standard price control, goods movements are valuated with a price that remains constant for at least one period. The standard price that is assigned to a material is usually the result of a standard cost estimate.
The main difference between the two valuation procedures is that the average price represents a current delivered price while thestandard price is based on planned values and not actual values. Differencs between the planned price and the actual prices are not assigned to the material stock in Financial Accounting, but rather are assigned to a price difference account. When using the moving average price, however, thematerial stock value in Financial Accounting can reflect the pricesactually incurred.
c) First-In, First-Out (FIFO) assumes that costs are used in the order in which the related goods were purchased. The cost of inventory at hand at the balance sheet date must therefore represent the most current purchase prices.
d) Last-In, Last-Out (LIFO) matches the cost of the last goods purchased against revenue.
The LIFO Reserve
Some companies use LIFO for tax and external reporting purposes, but they maintain a FIFO, average cost, or standard cost system for internal reporting purposes. The difference between the inventory method used for internal reporting purposes and LIFO is often referred to as the LIFO reserve. This is the allowance to reduce inventory to LIFO. The LIFO reserve is a contra-inventory account that must be adjusted to its required balance at the financial statement date.
RECORDING INTERVAL CAPABILITY
Inventory records can be maintained on a perpetual or a periodic basis. Conceptually, the perpetual inventory method provides a company with the capability of maintaining continuous records of the quantities of inventory and the costs flowing through the inventory accounts. The periodic method, on the other hand, requires counting the quantity of inventory before inventory records can be updated. In the past, manufacturers tended to keep perpetual inventories, while retailers used the periodic method. However, today a variety of modern point of sale devices and dedicated microcomputer software are readily available to provide any company with perpetual inventory capability.
Advantages of the Standard
Advantages of the Standard Price When using the standard price, all goods movements of a material arevaluated with the same price over at least one period. Therefore, thestandard price ensures consistent cost management of the productionprocess and makes variances within production transparent. A periodicprice (standard price) is especially useful when working with costmanagement by period. The standard price can also be used as a benchmark by which you canmeasure different methods of production, or compare the contributionmargins of a material in different market segments in ProfitabilityAnalysis. Disadvantages of the Standard Price Because the standard price is held constant for an entire period, it doesnot reflect the actual costs incurred during the period. This can lead toinexact valuation prices for materials whose procurement prices change agreat deal over a period, or whose method of production changes within aperiod. This problem increases in multilevel production with each new productionstep. This means that the costs for the finished product may not reflectthe most recent data. The material stock value does not reflect the current procurement costs,as variances from the standard price are collected in a price differenceaccount in Financial Accounting and do not lead to a correction of thematerial stock account. The variances collected in the price differenceaccount can no longer be assigned to the individual material. If you use split valuation for materials, please note that you can onlyrelease the material price at the header level of a material (not at thelevel of the valuation type) when calculating a material price in ProductCost Planning. Advantages of the Moving Average Price The advantage of using the moving average price is that variancesoccurring both for materials produced in-house as well as materialsprocured externally cause an update in the material price and the materialstock value. Because the material price reflects the average procurementcost of a material, material issues could, in principle, be valuated withthe current price. Only in special cases are variances allocated to a price differenceaccount in Financial Accounting rather than to the material stock. The advantages of the moving average price are seen only if: you arelooking at the material valuation data at the lowest production level; allvariances occur immediately; the material price is not distorted by thesequence of postings by the system. Disadvantages of the Moving Average Price The main disadvantage of using the moving average price is that the priceused to valuate a material consumption is almost completely dependent onthe time at which the goods issue is posted in the system. If, forexample, an invoice receipt is posted in the system after a goods issuewas entered, that invoice value is not reflected in the value of thematerial issued. The material is therefore not valuated with its actualprocurement cost. The moving average price also does little to guarantee consistent costmanagement of your production process. The effect of changes in theproduction process, for example, are not recognizable in the finishedproduct, and comparing results from different areas in ProfitabilityAnalysis is not really meaningful due to lack of a benchmark. The fact that the moving average price is not dependent on the period canalso lead to incorrect material valuation, as goods movements that areposted to a previous period are not valuated with the price from thatperiod, but rather with the current moving average price. Another problemwith the moving average price is that any mistake entering data can causeimmediate and unwanted changes in the material price. Any goods issuesposted following this error will be valuated immediately with thisincorrect material price. In particular, the moving average price can lead to unrealistic materialprices in cases of multi-level production or when there are variances thatdo not appear immediately. Such unrealistic prices occur, for example,when, in the context of stock coverage, a subsequent adjustment to thematerial stock occurs using an incorrect base quantity. For more informatin, see Valuation with the Moving Average Price.